Besil 8230-15 A/B Flame retardant Thermal Conductivity silicone potting compound
- Flame retardant UL 94-V0 elastomer
- Two-part, 1:1 mixingratio
- Medium viscosity Room temperature cure or rapid heat cure
- Addition cure system: no cureby-products
- Flame retardant: meets Underwriters Laboratories UL 94-V0
- Stable and flexible from -50°C(58°F) to +250°C (432°F)
- Flexible rubber – protects against mechanical shock and thermal cycling stress at components
- Excellent dielectricproperties
Besil 8230-15 A/B Flame retardant Thermal Conductivity silicone potting compound. It has good fluidity after mixing. The operating time can be adjusted according to the temperature. It can be deep-cured at room temperature. It is suitable for potting protection of various heat dissipation and temperature resistant components.
Characteristics before hardening
Test item | Test standard | Part A | Part B |
Appearance | Visual | Black viscous liquid | White viscous liquid |
Viscosity, CPS, 25 ℃ | GB/T 10247-2008 | 4800±1000 | 4500±1000 |
Specific gravity, g/cm3, 25℃ | GB/T 15223-1994 | 2.60±0.05 | 2.60±0.05 |
Mixing ratio | Mass ratio | A:B = 100:100 | |
Viscosity after mixing, 4# rotor, cps, 25℃ | GB/T 10247-2008 | 5000±1000 | |
Operation time, min, 25℃ | GB/T 10247-2008 | 30±10 | |
Initial cured time, min, 25℃ | GB/T 10247-2008 | 60±10 | |
Cured conditions | GB/T 10247-2008 | 25℃/6hr or 70℃/ 50mins, 80℃/ 30mins | |
Characteristics after curing | |||
Appearance | Visual | Gray flexible elastomer | |
Hardness, Shore A | GB/T 531-2008 | 24±5 | |
Thermal conductivity, W/mK | GB/T 10297-1998 | 1.50±0.05 | |
Elongation,% | GB/T 528-1998 | 65 | |
Shear strength, Al-Al | GB/T 6328-86 | 0.45 | |
Shear strength, PPS-PPS | GB/T 6328-86 | 0.26 | |
Coefficient of linear expansion,K-1,ppm | HGT 2625-1994 | 130 | |
Dielectric strength,kV/mm,25℃ | GB/T 1695-2005 | ≥20 | |
Volume resistance,DC500V,Ω·CM | GB/T 1692-92 | 1.1×1014 | |
Loss factor (1 MHz) | GB/T 1693-2007 | 0.01 | |
Dielectric constant(1 MHz) | GB/T 1693-2007 | 3.5 | |
Temperature range, ℃ | GBT 20028-2005 | – 60 ∽ 200 |
Application
- Automotive electronics, modules
- LED power drive module
- Solar module junction box
- Electric vehicle charging column module
- Lithium battery pack, capacitor pack
- Magnetic induction coil
- Inverter power supply
Operation process
- Before use, stir components A and B evenly in their respective packages, because the filler may partially settle during the storage process.
- Weigh the components A and B at A ratio of 1:1, mix them evenly, and directly inject them into the components (or modules). It is best to inject slowly along the side of the wall to reduce the generation of bubbles.
- After the bubbles disappear, it can be solidified by heating or directly solidified at room temperature, which takes about 8
- For quantitative glue filling equipment, please consult our Marketing Department.
TDS Download BeSil 8230
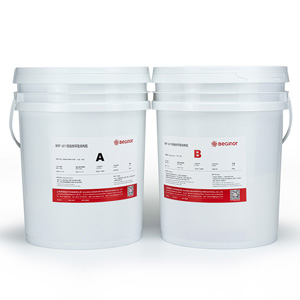
Color: black
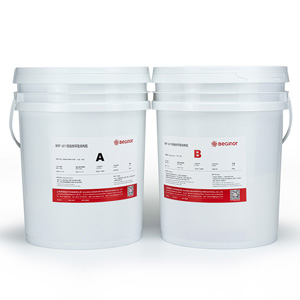
Color: black
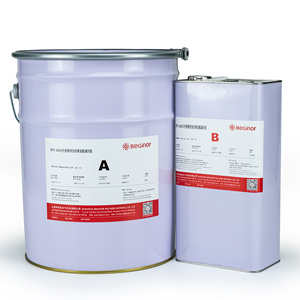
Color: black
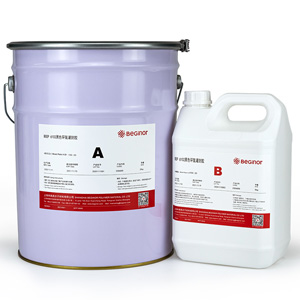
Color: black